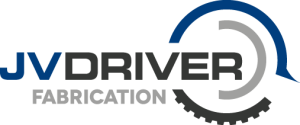
Our Fabrication Facilities
Welcome to the most technologically advanced, multi-discipline manufacturing and fabrication facilities in North America. We always think about being exceptional at what we do – and the JV Driver Group has applied a number of “Think Different, Build Better” innovations to how we think about industrial fabrication. We do what others can’t due to innovations in facilities and approaches. We conducted extensive research, visited facilities around the world and then embarked on a large investment program that has resulted in state-of-the-art facilities that allow for the most productive workflow. Simply stated our new facilities and tooling are among the most exceptional and most modern in the world. With over 420,000 square feet coupled with 100 acres for module erection and locations in Edmonton, Houston, Phoenix and Newfoundland we can offer our large capacity and broad capability to all major North American industrial and marine markets with the best in safety, quality and value.
Highlights
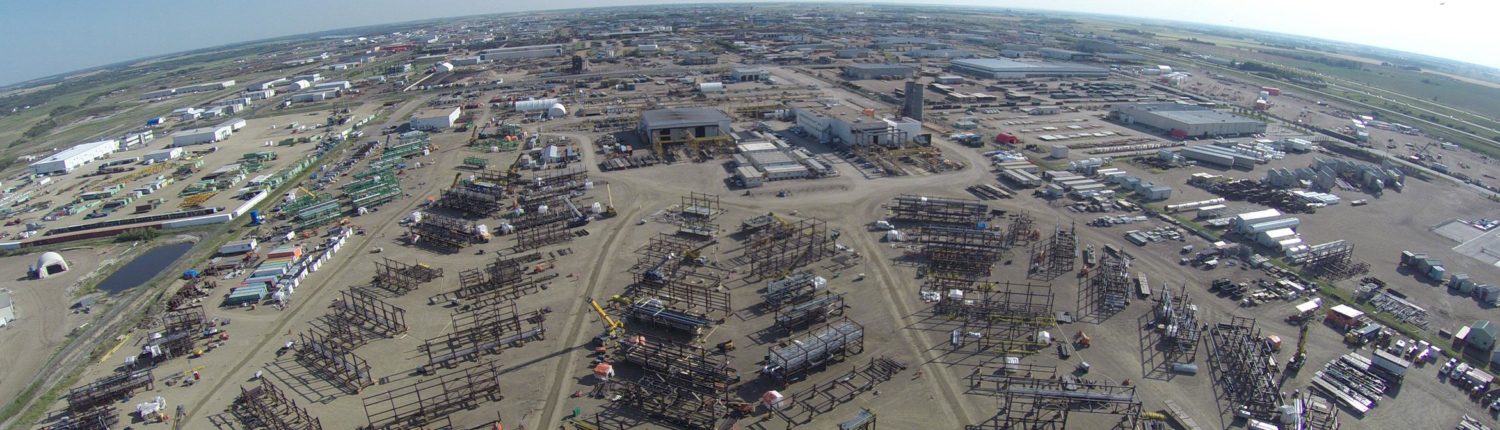
Nisku Facility
Our 80 acre, security patrolled site is a state-of-the-art facility that uses a unique “Single Site, Single Source” approach and was built with the future in mind.
We provide pipe fabrication, structural steel fabrication and module erection all under one roof, from start to finish. We fabricate structural steel and pipe before assembling in our module yard. This allows us to offer our clients a level of support, safety and efficiency that was previously unmatched at all areas of the project.
As a result of our success, we have opened a second facility in Phoenix, Arizona. Wherever you are in North America, we have a solution for you.
“Our professionalism in the industry and the people we work with sets us apart.” — Elval Rogers, Senior Operations Manager
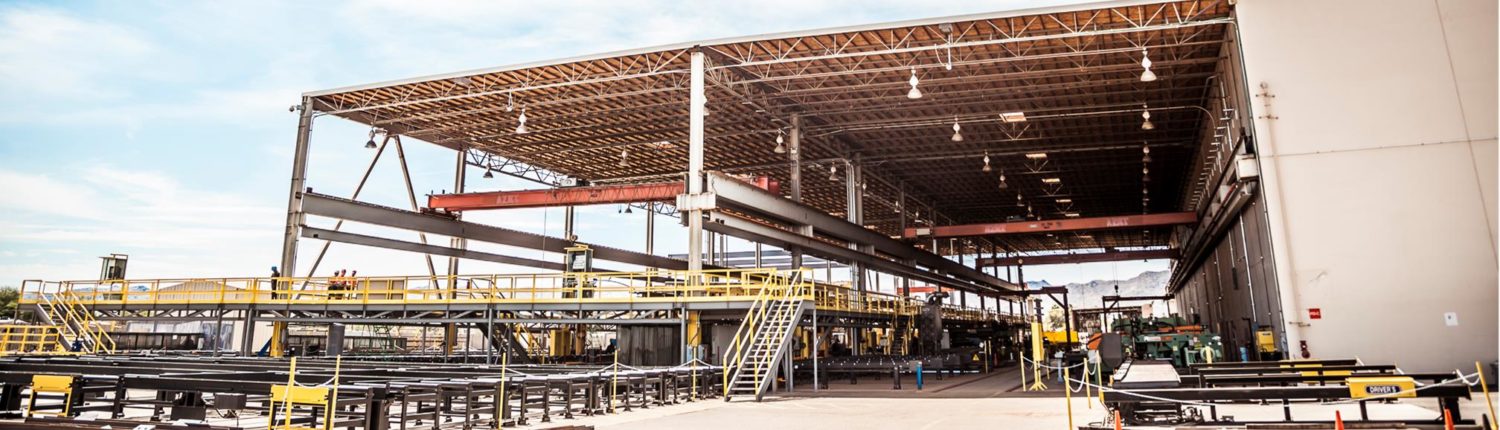
Phoenix Facility
JV Driver Fabricators Phoenix is a state-of-the-art fabrication facility in beautiful Phoenix, Arizona. This new facility mirrors our existing Albertan facility and effectively doubles our fabrication capacity for the North American construction market.
The 180,000 sq. ft. facility, built with safety and efficiency in mind, includes a 80,000 sq. ft. structural steel fabrication facility, a 50,000 sq. ft. pipe fabrication facility and an 18-acre module and skid assembly yard.
Located with easy access to the Interstate and boasting one of the biggest pipe fabrication facilities in the the Southwestern United States, our facility can maintain up to 350,000 inches of processed pipe per year and 20,000 tons of steel fabrication.
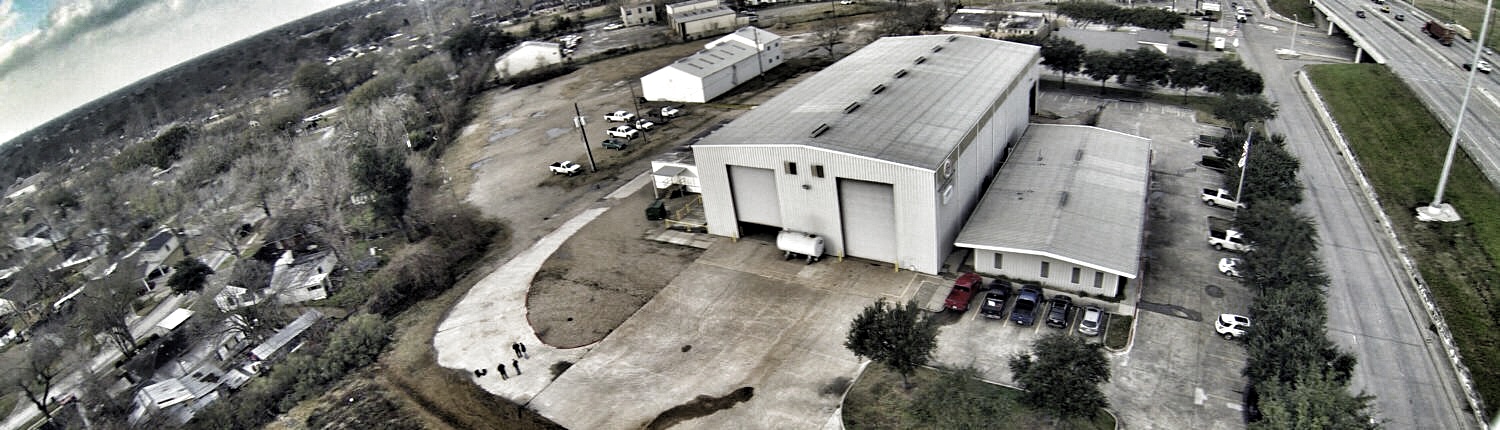
Houston Facility
Our structural steel fabrication facilities in both Edmonton and Phoenix are the result of years of research, planning and multiple facility visits around the world. Incorporating the most innovative steel fabrication processes and equipment in North America, including state of the art CNC processing equipment and innovative material management, RFID and GPS tacking, lean manufacturing and ground level innovations, our facilities are able to produce over 20,000 M/T of steel per year.
Our LEAN manufacturing shops are optimized at every step allowing materials to move seamlessly through the production process. Aided by state of the art conveyance systems and integrated material handling programming allows for minimal human interaction in material movement.
Supported by senior management, workers are empowered to create innovative solutions to any problems. These ideas lead to major efficiency gains, resulting in savings for our clients.
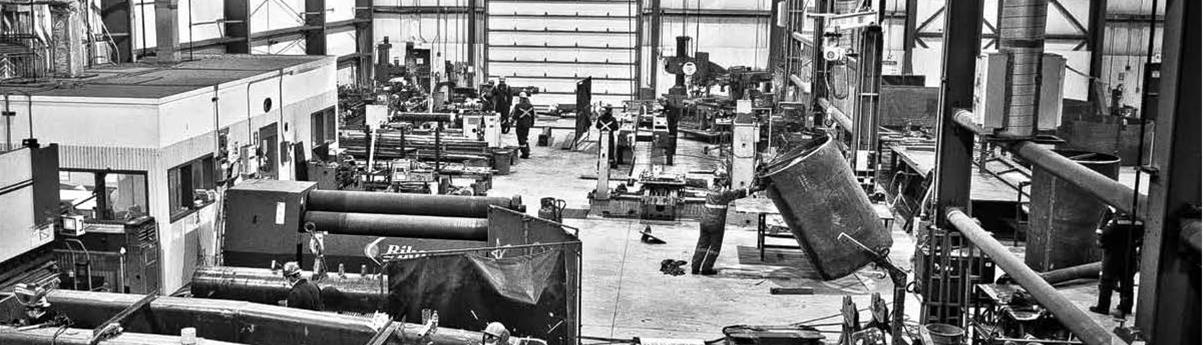
Newfoundland Facility
DF Barnes Fabrication was established in 2006 when DF Barnes identified manufacturing and export opportunities for advanced mechanical offshore and marine systems. Today, DF Barnes Fabrication offers contract manufacturing, machining and fabrication of complex structures and systems consisting of a variety of metals to clients worldwide.
DF Barnes Fabrication works out of 45 Pepperell Road. Increasing customer demand has led DF Barnes Fabrication to build this new state-of-the-art fabrication facility at this location. The Facility is 30,000 ft2 and includes a machine shop and custom fabrication and production area for carbon and specialty steel products. In addition, the facility has over 5 acres of secure, fenced lay down space.
DF Barnes Fabrication flagship product, the Launch and Recovery System (LARS), is used to launch and recover Remotely Operated Vehicles (ROVs) during offshore oil operations. These 30-feet-by-12-feet assemblies are fabricated from exotic steel and are used primarily by the offshore oil and gas industry. LARS are generally deployed in harsh environments, and therefore, require precise fabrication adhering to strict international standards. In addition to LARS, DF Barnes Fabrication manufactures traction winches and Temporary Guide Bases (TGBs), which are used for large subsea oil and gas structures.
In 2007, DF Barnes Fabrication won the Canadian Manufacturers and Exporters’ Canadian Innovation Award for Productivity Improvement and was named Newfoundland and Labrador’s Exporter of the Year in 2008.
What we Fabricate
DF Barnes Fabrication is manufacturing advanced mechanical and hydraulic systems for the world’s largest marine and offshore companies. With the continuous production of LARS, TGBs, and traction winches, DF Barnes Fabrication has established efficient manufacturing processes and extraordinary economies of scale. The company has implemented Lean Manufacturing principles, which are standard, formal procedures applied to contract manufacturing operations, that enable the company to manufacture to demand and lower costs of production by reducing waste. These lower costs of production are passed on to customers through low prices, which subsequently provide better value.
As an affiliate of DF Barnes, DF Barnes Fabrication employs a team of highly skilled and experienced personnel and management that are committed to providing superior quality, reliability, and service at competitive rates, while maintaining a safe, incident-free work environment. In addition, the company is continually working to improve its products and services to provide the best possible value for its clients.
Key Capabilities
-
- Subsea Equipment Fabrication/Repair
- Module Erection
- Pipe Fabrication
- Riser Storage, Maintenance and Recertification